Magnesium parts are typically attached using specific techniques and methods due to the material's unique properties. Magnesium, known for its lightweight and high-strength characteristics, is widely used in various industries, including aerospace, automotive, and electronics. Understanding the right attachment methods is crucial for ensuring the durability and functionality of magnesium components.
Magnesium alloys have gained significant popularity in modern manufacturing due to their excellent strength-to-weight ratio. However, working with magnesium requires specialized knowledge and techniques, especially when it comes to attaching or joining these parts. This article will explore the most effective methods for attaching magnesium components and provide insights into the best practices for ensuring strong, reliable bonds.
Whether you're an engineer, technician, or simply someone interested in material science, this guide will equip you with valuable information about the methods, tools, and techniques used for attaching magnesium parts. Let's dive in and explore the world of magnesium assembly!
Read also:Unveiling The World Of Nbergwx Twitter A Comprehensive Guide
Table of Contents
- Biography (Magnesium Overview)
- Attachment Methods for Magnesium Parts
- Welding Techniques
- Fastening Solutions
- Adhesives and Bonding Agents
- Comparison of Methods
- Industry Applications
- Challenges and Solutions
- Maintenance Tips
- Conclusion
Biography: Understanding Magnesium
What is Magnesium?
Magnesium is a lightweight, silvery-white metal that belongs to the alkaline earth metals group on the periodic table. It has an atomic number of 12 and is highly valued for its excellent mechanical properties. Magnesium is approximately one-quarter the weight of steel and two-thirds the weight of aluminum, making it an ideal choice for applications where weight reduction is critical.
Properties of Magnesium
Magnesium possesses several advantageous properties, including:
- High strength-to-weight ratio
- Excellent corrosion resistance when alloyed with other metals
- Good machinability and formability
- Outstanding thermal and electrical conductivity
These properties make magnesium suitable for a wide range of applications, from aerospace components to consumer electronics.
Attachment Methods for Magnesium Parts
When attaching magnesium parts, it is essential to consider the material's inherent characteristics, such as its low density and susceptibility to oxidation. Several methods can be employed to join magnesium components effectively:
- Welding
- Mechanical fastening
- Adhesive bonding
Each method has its advantages and limitations, which we will explore in detail in the following sections.
Welding Techniques
Types of Welding for Magnesium
Welding is a popular method for joining magnesium parts, but it requires careful consideration due to the material's reactivity. Some common welding techniques used for magnesium include:
Read also:Rip To Your Grandma But Im Different A Journey Through Cultural Identity And Personal Growth
- TIG (Tungsten Inert Gas) Welding
- MIG (Metal Inert Gas) Welding
- Friction Stir Welding
These techniques ensure strong, durable joints while minimizing the risk of oxidation and other defects.
Advantages and Limitations
Welding offers several advantages, such as:
- High joint strength
- Minimal material distortion
- Compatibility with complex geometries
However, welding magnesium also presents challenges, such as:
- High susceptibility to oxidation
- Difficulty in controlling heat input
Fastening Solutions
Mechanical Fasteners for Magnesium
Mechanical fastening is another effective method for attaching magnesium parts. Common fasteners used include:
- Bolts
- Screws
- Rivets
These fasteners are often made from materials compatible with magnesium, such as titanium or stainless steel, to prevent galvanic corrosion.
Best Practices for Fastening
To ensure successful fastening of magnesium parts, follow these best practices:
- Use compatible materials to avoid corrosion
- Pre-treat surfaces to improve adhesion
- Apply proper torque to avoid over-tightening
Adhesives and Bonding Agents
Using Adhesives for Magnesium
Adhesive bonding is a versatile method for attaching magnesium parts, offering advantages such as:
- Even stress distribution
- Excellent resistance to vibration and impact
- Minimal weight addition
Common adhesives used for magnesium include epoxies, polyurethanes, and acrylics.
Choosing the Right Adhesive
When selecting an adhesive for magnesium, consider factors such as:
- Chemical compatibility
- Curing time and temperature
- Environmental resistance
Comparison of Methods
Each attachment method for magnesium parts has its own set of advantages and limitations. Below is a comparison of the three primary methods:
Method | Strength | Weight Addition | Complexity |
---|---|---|---|
Welding | High | None | High |
Mechanical Fastening | Good | Minimal | Moderate |
Adhesive Bonding | Good | None | Low |
Industry Applications
Aerospace Industry
In the aerospace industry, magnesium parts are often used in aircraft components due to their lightweight nature. Welding and adhesive bonding are the most commonly used methods for attaching these parts, ensuring strong and reliable joints.
Automotive Industry
The automotive industry benefits from magnesium's weight-saving properties, utilizing it in components such as engine blocks and structural parts. Mechanical fastening is frequently employed in this sector to ensure durability and ease of maintenance.
Challenges and Solutions
Common Challenges
Attaching magnesium parts presents several challenges, including:
- Oxidation during welding
- Galvanic corrosion with incompatible materials
- Thermal expansion mismatches
Possible Solutions
To address these challenges, consider the following solutions:
- Use inert gas shielding during welding
- Select compatible materials for fastening
- Apply thermal management techniques
Maintenance Tips
Proper maintenance of magnesium components is essential for ensuring their longevity and performance. Follow these tips:
- Regularly inspect joints for signs of wear or corrosion
- Apply protective coatings to prevent oxidation
- Adhere to manufacturer guidelines for maintenance
Conclusion
In conclusion, magnesium parts are typically attached using welding, mechanical fastening, or adhesive bonding, each with its own advantages and limitations. The choice of method depends on factors such as application requirements, material compatibility, and environmental conditions.
We encourage readers to share their experiences and insights in the comments section below. Additionally, feel free to explore other articles on our website for more in-depth information on material science and engineering topics.
Thank you for reading, and we hope this guide has been informative and helpful!

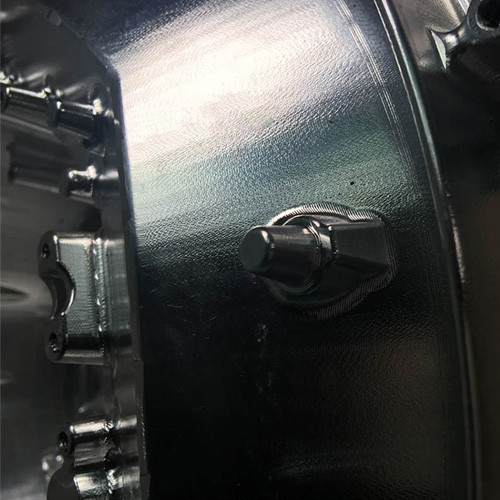
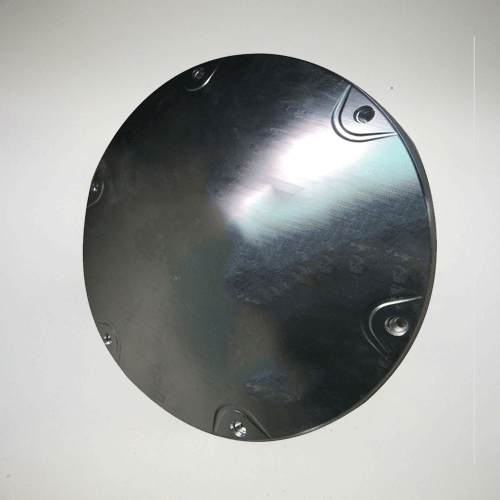